数控机床采用了先进的控制技术,是机、电、、液相结合的产物,技术先进、结构复杂。所以,出现故障后,诊断起来也比较困难。下面给大家介绍一些行之有效的数控机床故障诊断方法。
(1)了解故障发生的过程、观察故障的现象
当数控机床出现故障时,首先要搞清故障现象,要向操作人员询问故障是在什么情况下发生的,怎样发生的及发生过程。如果故障可以再现,应该观察故障发生的进程,观察故障是在什么情况下发生的,怎么发生的,引起怎样的后果,只有了解到第一手情况,才有利于故障的排除。常言说,把故障现象搞清楚,问题也就解决一半了。搞清楚了故障的现象,然后根据机床和数控系统的工作原理,就可以很快地确诊问题所在并将故障排除,使设备恢复正常使用。
举一个维修案例:一台采用美国BRYANT公司TEACHABLE Ill系统的数控外圆磨床在自动加工时,砂轮将修整器磨掉一块。为了观察故障现象并防止意外再凝发生,将砂轮拆下运行机床,这时再观察故障现象,发现在自动磨削加工时,磨材正常没有问题,工件磨削完之后,修整砂轮时,砂轮正常进蛤,而砂轮修整器旋转非常快,很快就压上限位开关,如果这时砂轮没拆,肯定砂轮叉要撞列修整器上。根据机床的工作尿理,砂轮修整嚣由E轴伺服电机带动,用旋转编码器作为位置反馈元件。正常情况下修整器修整砂轮时,Z轴滑台蒂动E轴修整器移动到修整位置,修整器做30-120度的摆动来修整砂轮。
仔细观察故障现象发现;E轴滑台在压上限位开关时,在屏幕上E轴的坐标值只有60度左右,两实际位置太概在180度左右,显然是位置反馈出现阚题,但更换了位控板和编码器都没有解决问题。又经过反复的观察和试验,发现E轴修整器在Z轴的边缘时,回参考点和旋转摆动都没有问题,当修整器移动到Z轴滑台中阀时,手动旋转就出现故障。
根据这个现象断定可能是由于E轴的编码器经常随修整器在z.轴滑台上往返移动,而使编码器的电缆电线某些线折断,导致电境随修整器的位置不同,在Z轴边缘时,接触良好,不出现故障,而在Z轴的中间时,有的信号线断开,将反馈脉砷丢失。基于这种判断,开始校砖编码器反馈电缆,发现确实有儿根线接触不良,找朝断线部位后,对断线进行焊接并采取防折措施,重新开机测试,故障消除,机床恢复了正常使用。
(2)直观观察法
就是利用人的手、跟、耳、鼻等感觉器官来查找救障原因。这种方法在数控机床故障维修时是非常实用的,下面介绍几种常用的方法。
①目测方法
目测故障板,仔细检查有无保险丝烧断,元器件烧焦,烟熏,开裂现象,有元异物、断路现象。以此可判断板内有无过流、过压、短路等问题。
②手摸方法
用手摸并轻摇元器件,尤其是阻容,半导体器件有无松动之感,以此可检查出一些断脚、虚焊等问题。
③通电观察
首先用万用表检查各种电源之间有无短路现象,如无即可接入相应的电源,目测有无冒烟,打火等现象,手摸元器件有无异常发热,以此可发现一些较为明显的故障,而缩小维修范围。
下面给大家举一个维修案倒:一台采用西门子810M的数控沟道磨床开机后有时出现11号报警,指示UMS标识符错误,指示机床制造厂家储存在UMS中的程序不可用,或在调用的过程中出现了问题。出现故障的原因可能是存储器模板或者UMS子模板出现问题。为此,首先将存储器模板拆下检查,发现电路板上A、B阍的连接线已腐蚀,接触不良。将这两点焊接上后,开机测试,再也没有出现这个报警。
再举一个维修案例:一台采用西门子810M系统的淬火机床一次出现故障,在开机回参考点时,y轴不走,观察故障现象,发现在让Y轴运动时,Y轴不走,但屏幕上Y轴的坐标值却正常变化,并且观察Y轴伺服电机也正常旋转,因此怀疑伺服电机与煞枉闯的联轴器损坏,拆开检查确实损坏,更换新的联轴器故障消除。
(3)根据报警信息诊断故障
现在数控系统的自诊断能力越来越强,数控机床的大部分故障数控系统都能够诊断出来,并采取相应的措施,如停机等,一般都能产生报警显示。当数控机床出现故障时,有时在显示器上显示报警信息,有时在数控装置上、PLC装置上和驱动装置上还会有报警指示。
另外机床厂家设计的PLC程序越来越完善,可以检测机床出现的故障并产生报警信息。
在数控机床出现报警时,要注意对报警信息韵研究和分析,有些故障根据报警信息即可判断出故障的原因。
举一个维修案例:一台采用FANUC 0TC.系统的数控车床,出现2043号报警,显示报警信息“HYD.PRESSURE DoWN(液压压力低)",提示,机床液压系统压力过低。根据报警信息对液压系统进行检查,发现液压压力确实很低,对液压压力进行调整后,机床恢复了正常使用。
而另一些故障的报警信息并不能反映故障的根本原因,而是反映故障的结果或者由此引起的其他故障这对要经过仔细的分析和检查才能确定故障原因,下面的方法对这类故障及没有报警的一些故障的检测是行之有效的。
(4)利用PLC的状态信息诊断故障
很多数控系统都有PLC输入、输出状态显示功能,如西门子810T/M和810D/840D系统DIAGNOSIS菜单下的PLC STATUS功能,FANUC 0C系统DGNOS PARAM软件菜单下的PMC状态显示功能,日本MITSUBISHI公司MELDAS L3系统DIAGN菜单下的 PLC-I/F功能,日本OKUMA系统的CHECK DATA功能等。利用这些功能,可以直接在线观察PLC的输入和输出的瞬时状态,这些状态的在线监视对诊断数控设备的很多故障是非常有用的。
数控机床的有些故障可以直接根据故障现象和机床的电气原理图,查看PLC相关的输入、输出状态即可确诊故障。
举一个维修案例:一台采用FANUC 0TC的数控车床,一次出现效悼,开机就出现2041号报警,指示X轴超限位,但观察X轴并没有超限位,并且X轴的限位开关也没有压下,但利用NC系统的PMC状态显示功能,检查X轴限位开关的PMC输入xo.0的状态为“1",开关触点确实已经断开,说明开关出现了问题,更换新的矛关后,机床故障消除。
再举一个维修案例:一台采用日本MITSUBISHI公司的MELDAS L3系统的,数控车床,一次出现故障,刀架不旋转。根据刀架的工作原理,刀架旋转时,首先靠液压缸将刀架浮起,然后才能旋转。观察故障现象,当手动按下刀架旋转的按钮时,刀象根本没有反应,也就是说,刀架没有浮起,根据机床电气原理图,PLC的输出Y4.4控制继电器K44来控制电压柜,电磁闲控制液压缸使刀槊浮起,首先通过Ne系统的PLC状态显示功能,观察Y4.4的状态,当按下手动刀架旋转按钮时,其状态变为“l",没有问题,继续检现,Y4.4控制的直流继电器K44的触点损坏,更换新的继电器后,刀架恢复了正常工作。
(5)利用PLC梯图跟踪法确诊故障
数控机床出现的机床侧故障是通过PLC程序检查出来的,PLC检测故障的机理就是通过运行机床厂家为特定机床编制的PLC梯形图(即用户程序),根据各种输入、输出状态进行逻辑判断,如果发现问题,产生报警并整显示器上产生报警信息。有些故障可在屏幕上直接星示出报警原因;有些虽然在屏幕上有报警信息,但并没有直接反映出报警的原因,还有些教障不产生报警信息,。只是有些动作不执行,遇到后两种博况砖跟踪PLC梯形图的运行是确认故障的很有效的办法,FANUC数控系统和MITSUB!SHI。数控系统本身就有梯形图显示功能,可直接监视梯形图的运行。而SIEMENS 3系统、810T/M系统、850系统、805系统、840C系统等因为没有梯图显示功能,对于简单的故薄可根据纸版梯形图,通过的状态显示信息,监视相关的输入、输出及标志位的状态,跟踪程序的运行,而复杂的故障必须使用缩程器来跟踪梯形凰的运行,以提高诊断故障的速度和准确性。
举一个维修案倒:一台采用西门子3TT系统的数控铣床,PLC采用西门子S513CB。这台机床一次出现故障,分度头不分度,但没有故障报警。根据机床的工作原理,这时首先将分度的齿板与齿条啮合,这个动作是靠液压装置采完成的,是由PLC输出;(控稍液压电磁阀Y104采执行的。连接机外缡程器PG685跟踪梯形霉的实对变化,PLC输出Q1.4的梯形图见图9,利用编程器观察这个梯形图,发现标志位F123,0触.有闭合是PLC输出Q1.4没有得电。
继续观察如图9所示的关于F123.0的梯形图,发现标志位F105.2的触点没有闭接着观察如图10所示的关于F105.2的梯形图,发现PLC输入110.2没有闭合是故障1本原因。PLC输入19.3、19.4、110.2、110.3连接四个接近开关,检测分度齿板和齿j否啮合,不分度时,由于齿板和齿轮不啮合,这四个接近开关都应谊闭合。现在110.2闭合,可能是机械部分或检测开关有问题,检查机械部分正常没有问题,检查检测开关,现接近开关已损坏,更换新的开关后机床恢复正常工作。

图9关于标志位F123.0的梯形图
根据如图13所示的电气原理图;PLC输入113.2连接的是检测落下的接近开关36PSl3,将分度装置拆开。发现机械装置有问题,不能带动驱动接近开关的机械装置运动,所以113.2始终不能闭合。将机械装置维修好后,机床恢复了正常使用。
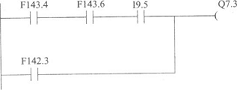
图3 PLC输入113.2的连接图
以上两种方法对机床侧故障的检测是非常有效的,因为这些故障无非是检测开关、继电器、电磁阀的损坏或者机械执行机构出现问题,这些问题基本都可以根据PLC程序,通过检测其相应的状态来确认故障点。
(6)机床参数检查法
数控机床有些故障是由于机床参数设置不合理或者机床使用一段时闯后需警调整,遇到这类故障将相应的机床参数进行适当的修改,即可排除故障。
举一个维修案例,一台采用FANUC OTC系统的数控车床在加工时,加工完工件的尺寸不稳。这台机床是在批量加工盘类工件的外圆,加工时发现有的工件外径尺寸超差。
对机床的刀塔、车刀进行检查设有发现再题,检查工装卡具也没有发现问题,工件的卡紧也正常。在检澍X轴滑台精度时发现X轴有0.04mm(直径疋寸)|的反向阎簿。
FANUC数控系统具有发现丝杠反向阀隙补偿劝能,参数PRM535为X。轴反向阈隙补楼参数,将谈参数从0改为2二。后,X轴反向间隙消除,这时工件加工尺寸基本不变。
再举一个维修案例:一台采用西门予840G系统的数控车床在蒋试加工新工件程序时出现报警。"2281 iST SOFTWARE LIMlrSWITCH MlNUS(第一轴超负向软件限位)",报警指示机床的第一轴——X轴超负向软件限位,为此首先检查屏幕上X轴的坐标鬟值显示为110mm,然后将机床数据调出进行检查发现X轴负向软件限位MD2280设置为110mm,所以当X轴运动到110mm时,系统就产生了超限位报警。, 对加工程序进行检查,加工该工件的程序设定X轴需要运动到108mm的位置,显然已超出软件灸向限位,对机床的行程进行检查,发现向负向运动逆有一定的余地,为此将机床数据MD2280从110mm修改封105mm,这时手动慢速移动X轴鲥106mm处,没有出现任何报警:重新运行新编捌的加工程序,正常运行不再出现ZZ8莲报警了。
(7)单步执行程序确定故障点
很多数控系统都具有程序单步执行功能,这个功能是在调试加工程序时使用的。当执行加工程序出现故障时,采用单步执行程序可快速确认故障点,从葡撵豫放薄。
举一个雄修案例:一台采用西门子810G系统的数控磨床,在瓤幕调试期间,外方技术人员将数控装置的数据清除,重新输入机床教据和程序后,进行调试,在加工工件时,一执行加工程序数控系统就死机,不能执行任何操作,关机重新启动后,还可以工作,但一执行程序艾死机。首先怀疑加工程序有问题。但没有检查出1问题,并且这个程序以前也运行过。当用单步功能执行程序时,发现每次死机都是执行到子程序L110的N220时发生的,程序 N220语句的内容为G18 D1,是调用刀具补偿,检查刀具补偿数据发现是0,没有进行谩置。根据机床要求将刀具补偿值Pl赋值10后,机床加工程序正常执行,再也没有发生死机的现象。
再举一个维修素例:一台采用FANUC 0TC系统姆数控车床出现报警"041 INTER-托RENCE iN CRC(CRe千涉)",程序执行中断。根据系统维护说明书关予这个报警的解释为,在刀尖半径补偿中,将出现过切削现象,采取的措施是修致程序。为进。步确认故障点,用单步功能执行程序,当执行到语句Z-65 R1时,机床出现报警,程序停止。因为这个程序已经运行很长时间;程序本身不会有什么问题,核对程序也没有发现错误:因此怀疑刀吴补偿有问题,根据加工程序,在执行上述语句时,使用的是四号刀二号补偿。重新校对刀吴补偿,输入后重新运行程序,再也没有发生故障,说明故障的原蹲确实是刀其补镂有问题。
(8)测量法
测量法是诊断设备故障的基本方法,当然对于诊断数控设备故障时也是常用方法。测量法就是使用万用表、示波器、逻辑测试仪等仪器对电子线路进行漏量。
举一个维修案例:一台采用西门子3G系统的数控磨床Z轴找不到参考点,这台机床在机床回参考点时X、Y轴回参考点时没有问题,但z轴回参考点时,出现辱限位报警,这时通过手动操作还可以将Z轴走回。
观察Z轴回参考点的过程,在压上参考点减速开关后,Z轴减速运行,但不停一直运动直到硬件限位开关才停止。
根据原理分析认为:可能编码器参考点脉冲有问题,没有发出脉冲或者脉冲幅值过低,用示波器检测编码器的参考点脉冲,一直没有捕捉到,怀疑编码器有问题,为此更换新的编码器,这时机床恢复正常工作。
(9)采用互换法确定故障点
对于一些涉及到控制系统的故障,有时不容易确认是哪一部分有问题,在确保没有进一步损坏的情况下,用备用控制板代换被怀疑有问题的控制板,是准确定位故瘁点的有效办法,有时与其他机床上同类型控制系统的控制板互换会更快速诊断故障。(这时要保证不会把好的板子损坏)。
(10)原理分析法
原理分析法是维修数控机床故障的最基本方法,当其他维修方法难以奏效时、可以从机床和数控系统的工作原理出发,一步一步地进行检查,最终查磁故障原因。
举一个维修案键名一台采用西门子810N系统的数控冲床,在长期停用后再启用时,通电后发现系统出规1号报警,指示后备电池没电,但更换电池后,1号电池报警仍消除不掉。根据两门予810N系统的工作原理,电池的电压信号接入电源模块,电源模块对电池电压进行比较判断,电压不足时产生报警信号,并传到CPU模块,从两产生报警。为此对电源模块进行核查,发现电池的电压信号在电源模块上的印刷电珞板的印刷电路连线腐蚀断路,所以不管电池电压如何,数控装置得到的信息都是电压不足,将线路板上腐蚀的连线用导线连接上后,机床恢复了正常工作。
以上介绍了维修数控机床故障的十种方法,在维修数控机床出现的故漳时这些方法往往要综合使用,有时单纯地使用某一方法很难奏效,这就要求维修人员具有一定的维修经验,合理弛。综合地使用这些维修方法,使数控机床能尽快地恢复正常使用。